CNC Machining Setup Software
There are considerably more opportunities to improve efficiency than to reduce a tool’s cycle time. All too often, manufacturing companies invest hundreds of thousands of dollars in new machine tools to increase production, or countless hours testing tools to take 30 seconds out of an operation, when they could accomplish more dramatic results with existing machinery at a fraction of the cost by using CNC Machining Setup Software.
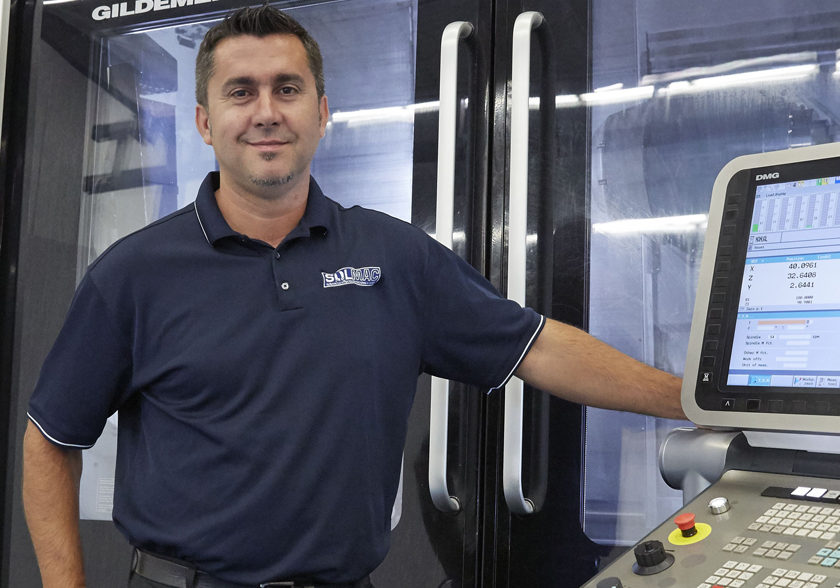
At shopGURU our customers are demonstrating a significant trend toward reducing the setup time involved in a machining operation – even when setting up the most complex parts.. We have found that many machines cut metal less than 50 percent of the time during working hours and even less in flexible manufacturing environments where part runs are generally short. For the rest of the time, these machines sit idle while their operators are setting up fixtures and tools for the next operation.
Some shops, unaware of the capabilities and cost efficiency of CNC Machining Setup Software like shopGURU , are missing out tremendously. For example, consider a shop running four CNC mills for two shifts per day at a shop rate of $40 per hour. If each operator takes only 1 hour per shift on each machine for tool setup, the shop is losing about $320 per day, or $83,200 per year, to spindle downtime. If this setup time isn’t sufficient to ensure optimal cutting conditions, short tool life and scrapped parts will quickly erode profits.
The key to boost production and output while increasing quality is REPEATABILITY of the setup and machining process.
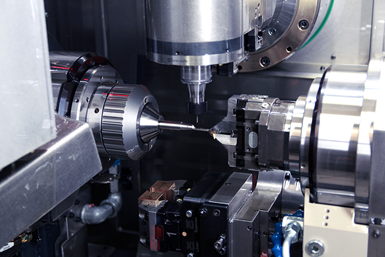
Many manufacturing operations go the traditional route of keeping a central tool crib and letting each machinist more or less fend for himself, gathering tools and then going back to his machine to execute the setup. We are seeing a significant shift by our customers when they use the Tool Crib that’s inside shopGURU to help the operator select the perfect tool in seconds. During the reduced setup time, part programs as well as tool offset data are recorded and replayed directly in shopGURU, reducing even further any possible human error.
The heart of the problem with the old way of doing things is that responsibility for getting fixtures and tools together for a job rested entirely with the machinists, and that simply has them spending too much time scrounging around the shop for everything they need to get a job up and running. When the machinist finally does locate everything he needs, each one of those tools has to be loaded into the machine and touched off manually to establish the initial tool offsets. Searching for and then setting the location of fixtures also significantly complicates a process that modular quick-change workholding rapidly solves. After all that time has elapsed, trial parts have to be carefully cut and closely examined to make sure the setup was ready for production.
Our customers have found that routine use of shopGURU with every part drastically reduces spindle downtime and keeps their machine tools producing quality components. Even more important, any level machinist can make the most complex parts, because with the ability to replay the setup and machining in shopGURU, there are no questions on how to make the job perfect.
As for the financial ramifications, there is little question that better management of setup time through Setup Software like shopGURU has added significantly to our user’s bottom line.
But not only that – it’s added to customer satisfaction which helps our users grow their businesses with confidence.
Curious what shopGURU can do for your shop? Request a free personalized demo at www.shopguru.com/demo today.
0 Comments